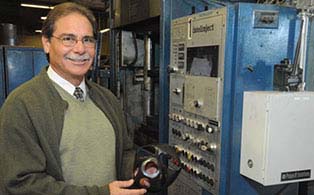
West American Rubber Company (WARCO) Rides On Energy Efficiency
West American Rubber Company received an incentive of more than $245,000 to install an energy management system using Automated Demand Response. They also participated in the Demand Bidding Program (DBP) and receive about $9,400 in demand response program credits annually. With Time-Of-Use rates and Critical Peak Pricing (CPP) events, it’s the perfect time to learn from WARCO’s energy-saving achievements and apply similar strategies to your business.
More Energy Management Success Stories
- Lamar Advertising Company raises visibility with LED energy efficiency project
- Jazz Semiconductor saved about $500,000 annually
- Merrick International decreased costs 35%
- Prime Wheel saved about $800,000 annually
- Allergan reduced 11% of its energy usage annually
- The Linde Group saved 1,100,000 kWhs annually
- Trojan Battery saved about $330,000 annually
- Quinstar Technology saved about $1,000 a month on their energy use
- Bravo reduced electric usage by nearly 750,000 kilowatt-hours
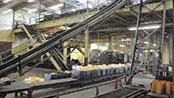
Shmaze Custom Coatings
This custom-painting shop received energy-saving equipment upgrades and earned $51,500 in incentives and demand response bill credits.

Essential Energy Technology for Manufacturers
Finance Your Energy-Efficient Projects
Several manufacturers have already taken advantage of energy-efficient equipment. To help your business receive these same cost-efficient benefits, we offer low-interest financing for qualified energy-efficient projects.
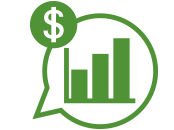
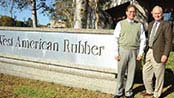
Energy-Efficient Solutions and Tips for Manufacturing
Here are just a few of the energy-efficient programs and suggestions that our customers have employed to increase their cost efficiency. You’ll also find more energy-efficient solutions in our Manufacturing Fact Sheet and a complete list of all our qualifying energy-efficiency incentives and demand response programs by requesting our Solutions Directory
Want to explore your clean energy options with SCE? We want to help lower your energy bill and reduce your carbon footprint. Clean energy can help provide the solution.
Motors and Compressors
With motors and compressors accounting for the majority of your energy use, here are some ways to control your costs.
- Install automatic shut-off devices to reduce peak demand
- Install small air compressors for low-use periods
- Install sequencing controls on multiple-unit compressor systems
- Install variable-frequency drives to control motor speed
- Replace old motors with high-efficiency motors
- Install new, water-efficient commercial equipment to minimize water demand
Your business may already qualify for incentives that could put these energy-saving upgrades into effect.
Lighting and Lighting Controls
Help improve your energy efficiency by better managing your lighting costs.
- Use LED bulbs and LED exit signs
- Install dimmable ballasts to lower energy use in fluorescent lamps
- Install inexpensive occupancy sensors
- Install sensory controllers on vending machines
There are many more energy-efficient solutions for your business.
Demand Response Programs (DR)
With these programs, receive bill credits for temporarily reducing energy use upon request during periods of high-energy demand. Choose the ones that best fit your operational needs.
Automated Demand Response (Auto-DR)
Receive energy savings by using smart technology that effortlessly and temporarily reduces the amount of energy your business uses (known as “load reduction”) during a DR event. With Auto-DR, load reduction is automatic and reliable, so it’s easier to participate in DR programs to capitalize on program earnings and help lower your energy costs.
- Install equipment that automates electrical load reduction during demand response events and receive Automated Demand Response Technology incentives
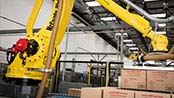
No-Cost, Do-It-Yourself Tips
Here are some immediate ways to significantly reduce your business energy use.
- Adjust employees’ schedules so energy-intensive production happens during TOU Off-Peak and Mid-Peak hours and before or after Critical Peak Pricing (CPP) events
- Adjust variable-speed drive controls for fans and pumps
- Reduce compressed air discharge pressure by 10 psi
- Repair air leaks in hoses and pipe connections to extend life of compressor
- Make comprehensive changes to industrial processes to reduce water consumption
- Change industrial process water system to reuse processed wastewater
- Reduce or shift production tasks away from TOU On Peak hours and during Critical Peak (CPP) events